Roof vulnerabilities
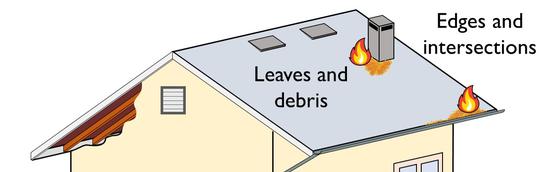
The roof protects the house from the elements. Its large surface area, however, makes it extremely vulnerable to embers during a fire. Specifically, debris can accumulate close to roof-wall intersections, edges, skylights, and vents, and ignite during a fire. Complex roofs, where the roof meets vertical walls (e.g., a roof with dormers, or a split-level house) present additional vulnerabilities that must be addressed. Roofs generally ignite at edges and intersections, so these areas should be prioritized.
How can you protect your roof?
Due to the wide variety of roof designs, here are some guidelines based on the different roof components.
Example | Vulnerabilities | Recommendations |
Edges and intersections ![]() ![]() |
Roof edges and intersections are vulnerable to wildfire exposures because of debris-filled gutter, or gaps between the roof covering and the roof sheathing. | Keep gutters clean of debris (see gutters section for more information). Repair damaged areas along roof intersections and install metal flashing in vulnerable areas (e.g. roof fascia). |
Valleys ![]() ![]() |
Two roof surfaces with different slopes create a valley. Valleys can be open (not covered by roofing materials) and closed. Leaves and debris can accumulate in these areas. |
The fire resistance of valleys can be improved by installing metal flashing (incorporating a mineral-surfaced cap sheet into the assembly). Metal flashing can be avoided with Class A asphalt composition shingles by interweaving the shingles (closed valley). |
Dormers ![]() |
Dormers create roof-to-wall intersections and can cause accumulation of leaves and debris in these areas. | An underlayment of fire-rated gypsum can increase the resistance to flame penetration (type X is a common gypsum board for this application). Protect intersections with metal flashing. Careful installation is crucial to avoid water damage. |
Skylights ![]() |
Skylights can provide an entry point for embers. Their vulnerability depends on slope of the roof, location and proximity of nearby vegetation, and accumulation of leaves and other debris around them. | If they can open, make sure they are shut during a wildfire. Keep skylights and surrounding area free of debris. Branches that overhang the skylight should be trimmed to prevent them from falling and breaking the glass or plastic. |
Roof vents ![]() |
Vents are extremely vulnerable to ember intrusion. The vents section discusses risks and mitigations in more detail. | See vents section for recommendations. |
Solar panels ![]() |
Properly installed panels on the roof do not increase the fire risk. However, panels can become vulnerable to wildfires if debris accumulates underneath them. | Regular removal of debris and roof maintenance will minimize the risk of ignitions nearby solar panels. |
What does fire rating mean?
Fire ratings for roof coverings are based on standard tests that evaluate three fire-related characteristics: 1) resist the spread of fire into the attic , 2) resist flame spreading on the roof covering, and 3) production of burning embers. Class A roofs provide the greatest protection, while Class C roofs provide the least. Non-fire retardant treated wood shakes are not rated (i.e., their rating doesn’t meet the requirements for Class C) and should not be used in wildfire prone areas. Class A materials include flat or barrel-shaped roof tiles, fiberglass asphalt composition shingles, and metal roofs (i.e., steel or copper). Fire-retardant pressure-treated shakes and shingles are the most common Class B roofing material. Class C fire rated roof coverings include recycled plastic and rubber products and roof aluminum coverings. Class B and C roof coverings can typically meet Class A requirements when additional underlayment materials are used.
Examples of Class A roof coverings: a) ceramic tiles; b) asphalt shingles; c) metal (steel) panels.
Details matter: stand-alone or assembly-rated?
Some roof coverings rely on an underlying material, or special installation techniques, to improve their fire rating. Fire ratings for roof coverings that require an additional material are typically referred to as a "by-assembly," as opposed to a "stand-alone," fire rating. Examples of a “by assembly” fire rating include fire-retardant treated wood shakes, aluminum and recycled plastic and rubber roof coverings. Common underlying materials include a mineral surfaced cap sheet (formerly referred to as a Type 72 cap sheet) adequate to provide Class A membrane construction, and a panelized fiberglass gypsum board.
The testing methodology is provided in the American Society for Testing and Materials (ASTM) Standard E-108, Underwriters Laboratory (UL) Standard 790, and National Fire Protection Association (NFPA) Standard 276. These standard test methods are similar, so there is no need to worry about which test was used to evaluate your roof covering.
Image from Quarles et al. 2010 (see additional resources).
California regulations
The roof covering should be built to prevent the intrusion of flames and embers. According to Chapter 7A of the California Building Code:
- Roofs shall have a roofing assembly installed in accordance with its listing and the manufacturer’s installation instructions.
- Where the roof profile allows a space between the roof covering and roof decking, the spaces shall be constructed to prevent the intrusion of flames and embers, be firestopped with approved materials or have one layer of minimum 72 pound (32.4 kg) mineral-surfaced nonperforated cap sheet complying with ASTM D 3909 installed over the combustible decking.
- Where valley flashing is installed, the flashing shall be not less than 0.019-inch (0.48 mm) No. 26 gage galvanized sheet corrosion-resistant metal installed over not less than one layer of minimum 72 pound (32.4 kg) mineral-surfaced nonperforated cap sheet complying with ASTM D 3909, at least 36-inch-wide (914 mm) running the full length of the valley.
Local additions to the code may exist in your community. Your local authorities can provide you with more information.
Products and assemblies that have complied with Chapter 7A can be found in the WUI Product Handbook. Since “ignition resistant” and “non-combustible” are performance-based characteristics (i.e., there is a standard test to show compliance), these materials are included in the Handbook.
Check out these additional wildfire preparedness resources from UC ANR Fire Network Members and our colleagues!
Home Hardening